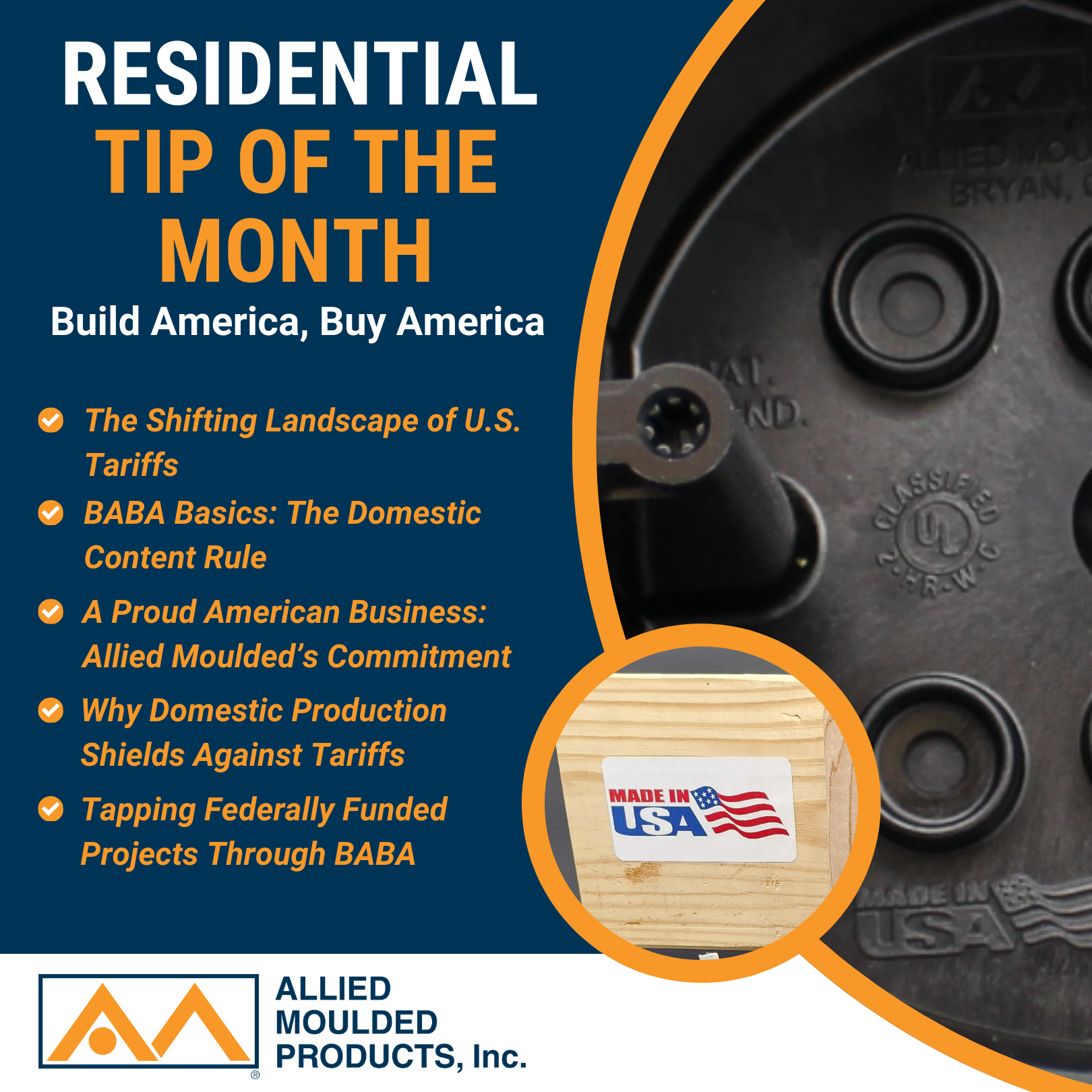
Building in the U.S. is a vehicle for job creation and economic growth. That’s why the Build America, Buy America Act (BABA) is a cornerstone for manufacturers who want to supply federally funded projects: It ensures that domestic materials become a requirement for certain projects.
Yet with tariffs and trade policies fluctuating at a seemingly endless pace, meeting BABA standards brings an extra layer of reassurance.
Below, we’ll explore why BABA compliance is so vital for a manufacturing business—especially one committed to American-made principles—and share how Allied Moulded exemplifies this strategy.
The Shifting Landscape of U.S. Tariffs
Over the past decade, tariffs have fluctuated dramatically. One year, imported metals might face a modest duty; the next, rates can skyrocket due to policy changes or global trade disputes.
For companies that hinge their entire production on foreign components, those surprises can be crippling.
They might find themselves suddenly uncompetitive on price, or scrambling to find alternative suppliers—and each day lost in that scramble pushes them closer to missed deadlines and unhappy customers.
BABA (part of the Infrastructure Investment and Jobs Act) counters this uncertainty by laying out clear-cut rules for domestic sourcing. If your construction materials qualify as “domestic,” you avoid the complexities of changing import duties and can more easily bid on projects that tap federal funding.
But BABA compliance isn’t just about meeting a code; it’s about ensuring supply chain stability and showing that you stand behind American workers and standards.
BABA Basics: The Domestic Content Rule
BABA typically requires that certain infrastructure materials are not only manufactured in the U.S., but that over 55% of their component costs originate domestically—or they meet the definition of a COTS (commercially available off-the-shelf) item that’s produced entirely in America.
For companies like Allied Moulded, which invests heavily in domestic production, this threshold is a natural fit.
Meeting those criteria is a direct ticket to reduced vulnerability whenever new tariffs hit. If your critical components come from a local source, you don’t have to worry about an unexpected spike in duties caused by international politics. Instead, you maintain predictable costs and lead times, crucial factors for delivering on big contracts.
A Proud American Business: Allied Moulded’s Commitment
At Allied Moulded, we believe in the value of American-made craftsmanship—from the design and engineering stages to final production. By manufacturing a vast range of nonmetal enclosures and boxes, and accessories right here in the U.S., we keep a tight grip on quality, cost, and speed.
But the real competitive edge emerges when potential or existing tariffs threaten to shake up the market.
Suppose there’s a sudden jump in import taxes on certain plastic components or hardware. That might cause headaches for foreign-based suppliers or domestic companies reliant on overseas raw materials. Yet for a fully committed U.S. manufacturer—one that sources components locally—the shift is far less disruptive. With your supply chain anchored domestically, cost and inventory remain stable, letting you deliver consistent value to your customers.
Bringing Nail Manufacturing In-House
To illustrate just how dedicated Allied Moulded is to securing supply chains and controlling costs, consider the story of our nails.
Historically, many manufacturers rely on third-party suppliers for nails, screws, or other small fasteners. When global steel prices soared or tariffs on metal imports rose, businesses found themselves facing sudden cost spikes or supply shortages.
Allied Moulded took a proactive step. We decided to bring nail manufacturing in-house. This wasn’t just a small-scale move: We’re now producing over 90 million nails per year—a volume that demonstrates our belief in local production. By doing so, we reduce dependency on overseas steel fluctuations, cut out middleman costs, and keep a closer eye on quality control.
The result? We can pass consistent pricing on to our customers, ensuring that enclosures and electrical boxes remain competitively priced—even if global metal markets start to whipsaw. Moreover, we create more American jobs and reinforce the ethos that underpins BABA compliance: Build America, Buy America.
Why Domestic Production Shields Against Tariffs
It’s not uncommon to see entire product lines rendered unprofitable overnight due to a new duty on crucial components.
For instance, a company relying on imported nails or metal rods might see a 25% tariff added suddenly, forcing them to either absorb the cost or hike prices—both undesirable scenarios.
Allied Moulded avoids this predicament by:
- Sourcing Domestic Inputs: Whether it’s resin for our fiberglass enclosures or nails for mounting hardware, we either manufacture in-house or partner with domestic suppliers.
- Streamlined Logistics: Shorter shipping routes from local suppliers mean fewer logistics snags and minimal freight cost increases, no matter how global fuel prices or shipping fees fluctuate.
- Stable Lead Times: No delayed cargo ships or customs inspections bottlenecking our production schedule. Domestic production flows more predictably, so we meet deadlines.
All these advantages feed into a simple yet powerful truth: a stable supply chain is vital in times of tariff volatility. By focusing on domestic content, Allied Moulded grants both itself and its customers a buffer against market upheavals.
Tapping Federally Funded Projects Through BABA
So how does BABA compliance unlock bigger opportunities?
In many federal, state, or municipal construction jobs—particularly those financed through infrastructure bills—the awarding bodies specify strict “Buy America” or “BABA” clauses. If you can’t prove your products meet domestic rules, you’re disqualified from the get-go.
For Allied Moulded, that’s a non-issue. Our enclosures and accessories are recognized as “domestic construction materials” for BABA compliance, meaning contractors can confidently list them in bids.
This opens doors to large-scale highway projects, water treatment facility upgrades, and expansions of public utilities, among other critical infrastructure ventures. With billions of dollars earmarked for upcoming infrastructure repairs and new builds, ensuring you have a certified domestic product line is a major advantage.
Looking Ahead: More Than a Requirement
While BABA is the current legislative driver, the principle behind it won’t vanish even if future laws shift.
By embedding domestic sourcing and in-house production at every level, a company can adapt more readily to unforeseen disruptions, from tariff wars to global shipping crises.
Allied Moulded has long been at the forefront of this approach. We see domestic content not just as a box to check for compliance, but as a blueprint for delivering consistent, high-quality products our customers can rely on.
As the U.S. continues to invest in infrastructure—from roads and bridges to broadband networks—companies that meet Build America, Buy America requirements stand in a prime spot to benefit. The unpredictability of tariffs can’t be dismissed, but by rooting production in domestic soil, a manufacturer lowers its risk and enhances its appeal to government contracts.
Allied Moulded exemplifies this. We’ve chosen to produce essential components at home, even something as ostensibly small as nails—manufacturing over 90 million every year in-house. That dedication to American-made goods, stable supply chains, and BABA compliance sets the foundation for thriving in a world where policies and import duties shift without warning.
If you’re a contractor, facility manager, or procurement official looking for reliable, made-in-America electrical boxes and accessories, Allied Moulded is ready to stand shoulder to shoulder with you. By selecting domestic solutions, you gain a strategic advantage on federal projects, cushion yourself against tariff upheaval, and support the spirit of American manufacturing—one electrical box (and one nail!) at a time.