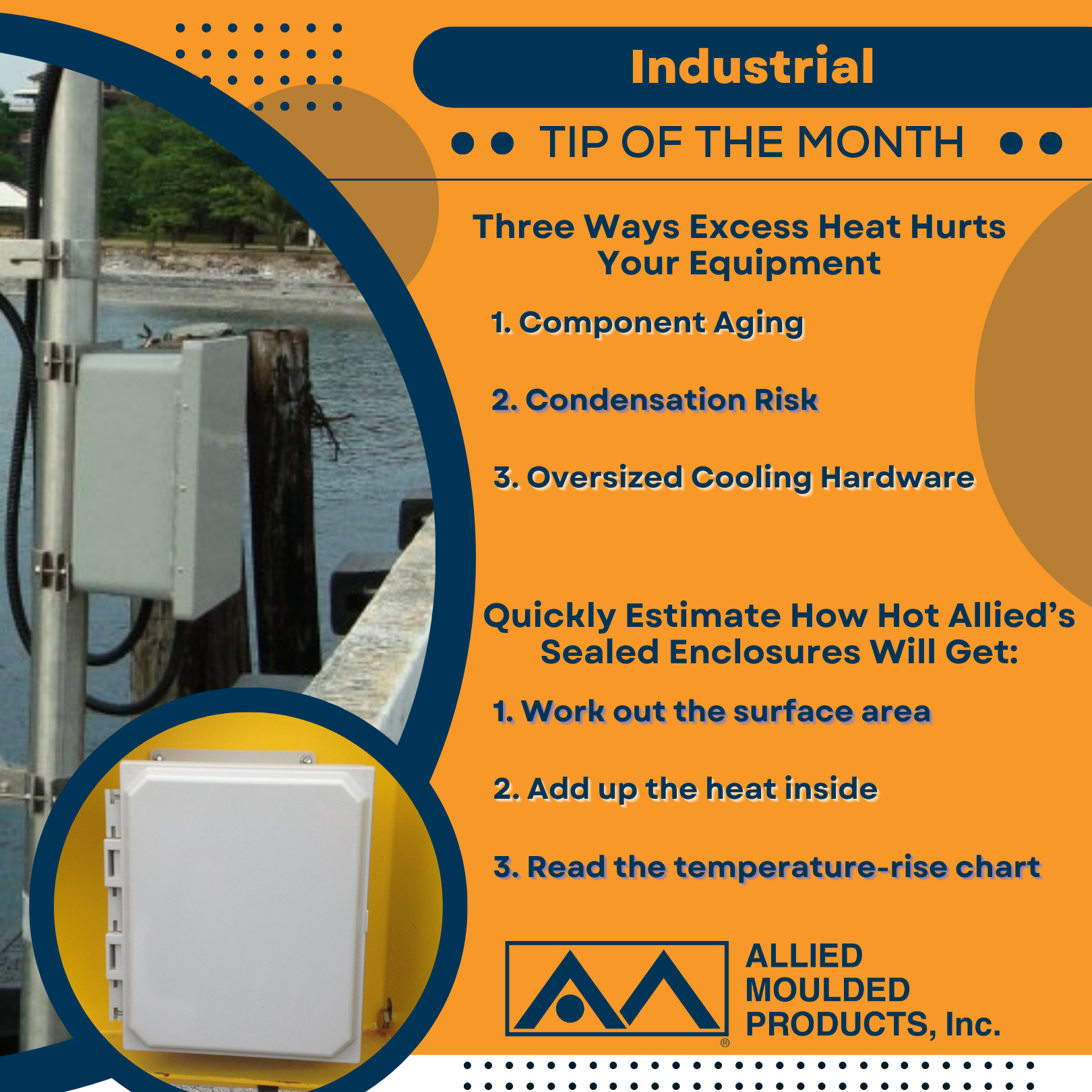
Walk a plant floor on a summer afternoon and you may notice something that’s easy to overlook: stainless-steel electrical enclosures absorbing machinery heat like mirrored ovens.
Inside, temperatures creep well past component ratings, silently shaving years off capacitors and forcing variable-frequency drives to derate. Most engineers focus on ingress protection and corrosion, but thermal behavior is just as critical.
To mitigate this important effect on your electrical enclosures, Allied Moulded prioritizes fiberglass products.
A Quick Look at Material Physics
Heat always moves from warm to cool, and the speed of that transfer hinges on thermal conductivity.
Stainless steel conducts heat roughly 50 times faster than fiberglass-reinforced polyester (FRP). In practice, that means a stainless wall can “pull in” exterior heat more quickly, then hold it like a warming plate. FRP’s glass fibers and resin, by contrast, create natural insulation that slows heat flow in either direction.
Rule of thumb for specifiers:
- A stainless enclosure can see about a 1.8°F internal rise for every watt of electronics heat per square foot of surface. An equivalent fiberglass enclosure might see heat rise only 0.036°F in those same conditions.
Three Ways Excess Heat Hurts Your Equipment
Component Aging
Capacitors and semiconductors—the workhorses inside drives, PLCs, and power supplies—are relentlessly temperature-sensitive. Most electrolytic capacitors follow the “18°F rule”: for every 18°F rise above their rated baseline (often 104°F), service life halves.
Push a cabinet from 122°F to 158°F and a capacitor designed for ten years may die in under three.
Transistors and diodes suffer, too; higher junction temperatures accelerate electromigration and degrade silicon dice, leading to random drive trips or outright board failure. In plants running 24/7, that means unplanned outages, expedited board replacements, and a spike in mean-time-between-failure metrics your reliability team tracks.
Here’s the recurring problem: Stainless walls act like heat sinks: they suck in solar and process heat, store it, and radiate it straight onto drives, PLCs, and power supplies.
Fiberglass flips that script. With a thermal conductivity significantly lower than stainless, it throttles external heat before it reaches sensitive electronics and lets internal heat bleed away more gently. Cooler, steadier air means capacitors stay hydrated, silicon stays below its critical temperature, and nuisance trips practically disappear, delivering extra years of reliable uptime for the price of choosing a different wall material.
Condensation Risk
This is a big one, especially in environments like water or wastewater treatment plants. Electronics hate moisture even more than heat.
A stainless box can hit 140°F in full sun, then cool to 68°F overnight. Warm air inside holds more water vapor; as the cabinet cools, that vapor reaches dew point and condenses on the coldest surfaces—usually PCB traces and terminal screws. Tiny water films create leakage currents that cause false sensor readings, nuisance resets, and eventually corrosion of copper pads. Once corrosion starts, it’s self-feeding; even a humidity spike on a rainy morning can re-activate the process, shortening board life by years.
Stainless, with its high conductivity, follows any drop in ambient/external temperature quickly. Humid air trapped inside can’t shed moisture fast enough and water condenses on the coldest metal surfaces—usually PCB traces and terminal screws—inviting short circuits and creeping corrosion. That self-feeding oxidation spreads under gaskets and compromises the NEMA seal you paid for.
Fiberglass’s insulating nature dampens that temperature swing. Interior walls cool more slowly, rarely crossing the dew point, so humidity stays in vapor form instead of dripping on circuitry. Even if a few droplets form, FRP won’t rust or pit, so there’s no oxidation site to spread. The result is drier boards, brighter terminals, and a maintenance routine that involves visual checks instead of desiccant packs and corrosion-inhibitor sprays.
Oversized Cooling Hardware
If your material choice forces the enclosure temperature up, the “fix” is usually to bolt on larger fan trays, louvers, or even full HVAC units. Those add:
- Capital cost (bigger chillers, NEMA fan kits, filters).
- Energy draw: a 300W fan running non-stop costs roughly $300/year in electricity (at $0.11 kWh).
- Maintenance load: filters clog, condensate drains block, and every fan bearing will fail eventually. In many cases, the extra cooling gear outprices the small premium of specifying a thermally superior fiberglass cabinet in the first place.
When a stainless enclosure runs hot, the typical fix is to bolt on bigger fan trays, louvers, or even compressor-based AC units. Those add capital cost, draw energy around the clock, and pile new tasks onto the maintenance calendar—filter swaps, bearing lubes, coil cleanings. Over a single cooling season, the electricity alone can cost more than the premium for a thermally superior enclosure.
Start with fiberglass and the heat load shrinks. Many FRP boxes need nothing more than a passive vent or a low-CFM fan mounted in factory-molded bosses—no drilling that risks your NEMA 4X/IP66 rating. Less hardware, lower bills, and no emergency service calls: that’s the compound return of choosing fiberglass on day one.
Conclusion
Shiny stainless looks tough, but it turns into a heat sink the moment sun or process equipment warms it up.
With natural insulating properties, Allied Moulded fiberglass enclosures help electronics stay within their comfort zone; no oversized air conditioners or derated drives required. Keep your cabinets cool, your gear stable, and your maintenance team off the emergency call list.
***SIDENOTE***
Need a quick estimate of how hot a sealed Allied Moulded fiberglass cabinet will get?
Just follow three basic steps.
- Work out the surface area.
Measure the box (height = A, width = B, depth = C in inches).
Plug those numbers into:
2 × [(A × B) + (A × C) + (B × C)] ÷ 144
The answer is the cabinet’s outside area in square feet.
- Add up the heat inside.
Look at every drive, power supply, and PLC going in the box and total their heat loss in watts (the spec sheets list this).
Divide that watt total by the surface area you just calculated. This gives watts per square foot.
(If someone gives you Btu instead of watts, remember 1 W = 3.413 Btu/hr.)
- Read the temperature-rise chart.
Match your watts-per-square-foot number to Allied’s chart. The chart tells you how many degrees the air inside will climb above the room temperature.
Example: A size AM30240RT enclosure (30 in × 24 in × 11.75 in) has roughly 18.8 ft² of surface. Put 200 W of electronics inside, and you get about 10.6 W/ft². The chart shows that density equals a 47°F rise.
If that rise pushes internal parts over their limits, plan on passive vents, a fan kit, or a larger cabinet.