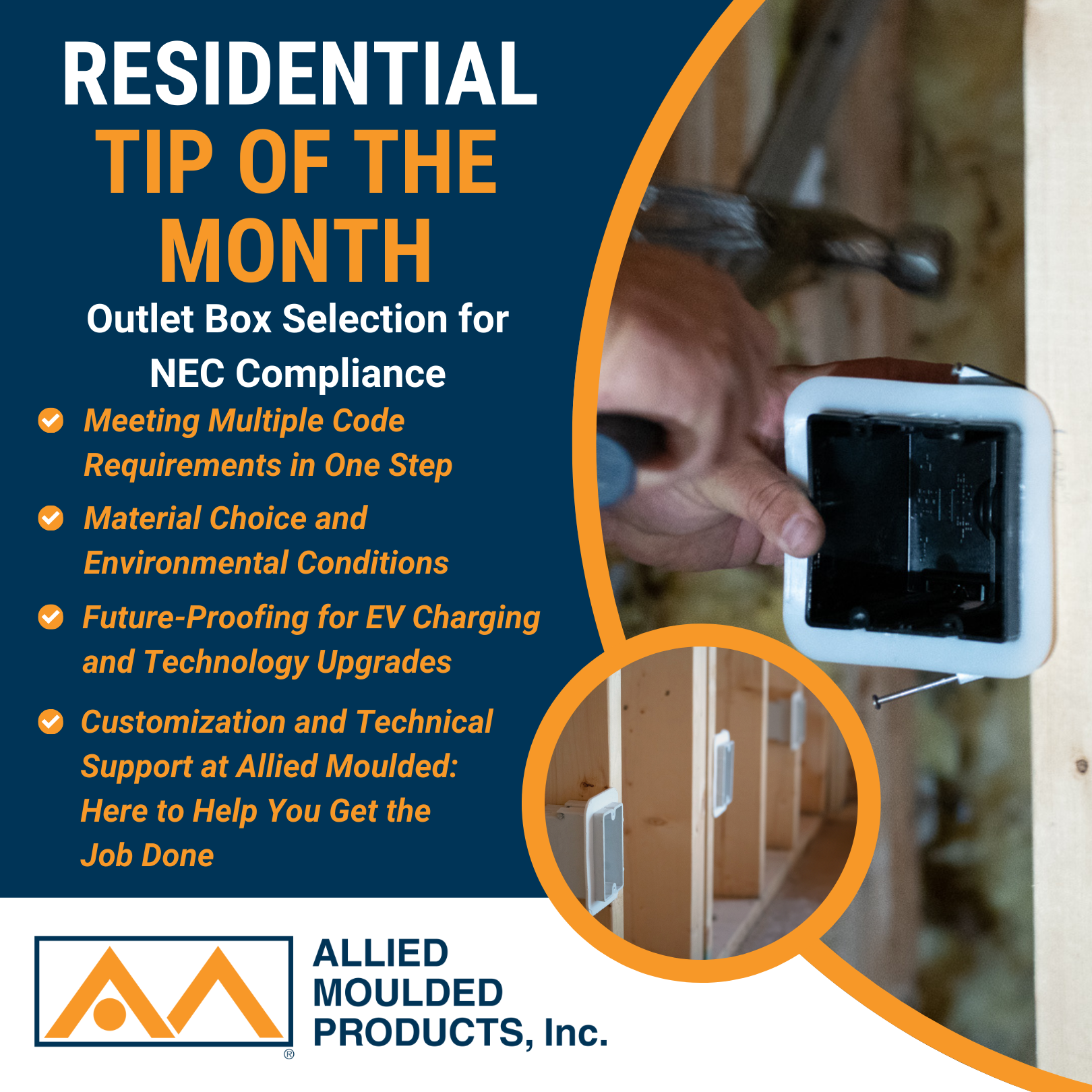
Ever had an inspection held up because an outlet box didn’t meet code?
Or had to rip out and replace several boxes after discovering they weren’t rated properly for the environment?
Getting box selection right the first time is an easy way to sidestep costly rework and keep projects on schedule.
Electrical enclosures and outlet boxes do far more than just contain wiring and breakers, of course: They’re integral to meeting many of the NEC’s ongoing updates—from expanded GFCI protection and updated arc flash labeling in 2025 to new surge protection mandates.
If you specify boxes early and align them with the project’s code requirements, you can streamline inspections, reduce retrofitting headaches, and ensure the final build stays on schedule.
Our brief guide explains why box selection is critical and how Allied Moulded’s lineup can address these complex needs.
Meeting Multiple Code Requirements in One Step
GFCI & Moisture Management
Think bathrooms, basements, and outdoor spaces: The current NEC now demands broader Ground-Fault Circuit-Interrupter (GFCI) coverage, including receptacles located in damp or wet areas (e.g., basements, laundry rooms, outside patios). The latest update covers 125–250 volt receptacles in even more locations.
Bathrooms have a broader definition (the entire area, even if partitioned), and garages plus accessory buildings now have no exceptions for GFCI. This means if you’re building large multi-bay garages or including detached storage units, every receptacle must have GFCI protection regardless of voltage or intended use.
For contractors, the cost and complexity of wiring can rise slightly, but the payoff is reduced risk of electrical shock incidents. Make sure you’re spec’ing GFCI receptacles or breakers early on, and double-check with local inspectors on how strictly they interpret the new bathroom and garage rules.
Fiberglass enclosures and outlet boxes inherently resist moisture absorption. They’re less prone to warping or corroding compared to metals, which can prolong box life and simplify compliance with GFCI device installations.
Arc Flash Labeling & Internal Safety
Contractors must now display more detailed hazard information—like incident energy and approach boundaries—directly on or near electrical equipment.
Enclosures can be custom-labeled or ordered with pre-printed arc flash or hazard warnings–seek this out in your purchase orders. This relieves the burden on your electricians, who would otherwise produce and apply labels themselves, and helps you avoid labeling errors that could fail inspection.
While NFPA 70E is the primary reference for arc flash safety, the NEC’s new labeling provisions ensure that contractors can’t overlook this step. Coordinate with your electricians or a safety consultant to ensure accurate label formats. Failing to provide correct arc flash markings may lead to inspection delays or, worse, put workers at unnecessary risk.
While the current NEC language calls out building sites other than homes, GCs should understand those risks. (For those non-home sites, any electrical service equipment or feeder-supplied equipment rated at 1,000 amps or more must have a permanent arc flash warning label. This label can be applied in the factory or added on-site and must follow industry standards. It also needs to include the date it was applied and meet the labeling rules outlined in 110.21(B).)
Surge Protection Integration
The current NEC makes SPDs (Surge Protective Devices) compulsory in many residential buildings using feeders, which includes apartments and condos.
Pursue boxes that will allow for convenient integration of surge protective devices, providing enough space and properly placed knockouts to ensure optimal SPD performance and easy conduit routing.
Material Choice and Environmental Conditions
Why Fiberglass?
Environment matters, so make sure you take a holistic approach to product sourcing throughout your job. For coastal or high heat and humidity projects, fiberglass boxes won’t warp or distort in high heat.
Then there’s the actual job site. Fiberglass is rigid and stands up to bumps and dings in your day-to-day work—important if your electricians are mounting enclosures in tight or awkward spaces. (And the current NEC refines working space dimensions (per NEC 110.26 and related sections) to accommodate larger, more modern equipment. Updated rules specify minimum depths, heights, and widths around panels to allow safe maintenance and clear egress.)
Lastly, fiberglass is an insulator, not a conductor like metal, making it safer to work around. And since fiberglass won’t oxidize or corrode over time, your wiring and connectors stay safe and protected.
Outdoor and Rooftop Applications
Rooftop mechanical rooms and exterior-mounted breaker boxes face intense sun exposure. Fiberglass formulations include UV inhibitors that guard against sunlight degradation.
And, again, bear in mind your environment, especially for those outdoor applications: In northern climates with freeze/thaw cycles or southern deserts with sustained heat, fiberglass-based enclosures often maintain structural integrity and keep interior electronics at safer operating temperatures.
Future-Proofing for EV Charging and Technology Upgrades
Extra Mounting Points and Space
Installing a Level 2 or Level 3 charger may require additional contactors, relays, and monitoring modules. Space matters. Allied Moulded outlet boxes and enclosures, especially larger models, offer ample panel space for these components.
Oversized or multiple knockouts allow you to run heavier-gauge cable or accommodate expansions later, ensuring you won’t need a complete box swap if your client decides to add more chargers.
Network and Monitoring Gear
Multifamily developments increasingly integrate sensors, submetering, and IoT (Internet of Things) modules that require a well-organized control enclosure.
Seek a partner like Allied Moulded that can furnish mounting back panels that hold PLCs, circuit boards, or data-logging hardware—future-proofing your setup for eventual software or firmware upgrades.
Customization and Technical Support at Allied Moulded: Here to Help You Get the Job Done
- Engineering Expertise
- If your project requires unique cutouts, hinged windows, or integrated surge modules, Allied Moulded’s team can advise on optimal enclosure configurations. This ensures a tight fit for your equipment without compromising integrity or code compliance.
- Pre-Assembly Options
- In some cases, Allied Moulded can pre-assemble or partially assemble back panels, special latches, or labeling systems before the enclosure ships. By reducing on-site assembly time, you shorten the overall installation window and improve quality control.
- Rapid Prototyping for Large Developments
- Multifamily projects, as an example, often repeat floor plans across dozens or even hundreds of units. Allied Moulded can provide rapid prototypes of a standardized outlet box layout so you can confirm fit, finish, and compliance before committing to a larger production run.
- Consulting on NEC Updates
- The company stays abreast of code changes, ensuring that recommended outlet boxes align with new requirements for GFCI, surge protection, and EV accommodations. Their reps can walk your team through these critical points so you specify the right gear from the start.
Putting It All Together
- Code-Driven Selection: By choosing boxes that tick multiple NEC requirements—GFCI-ready, surge-friendly, and arc flash-compliant—you spare yourself from chasing separate fixes.
- Durability & Environment: Fiberglass stands up to damp basements, seacoast air, and rooftop sun, maintaining box performance over the long haul.
- Future-Proof Design: As demand grows for EV charging and advanced building controls, a box that supports additional breakers or modules avoids big retrofits later.
Ultimately, selecting the right outlet box or enclosure under the 2025 NEC is about proactively fulfilling multiple requirements that protect your workers and secure your building’s electrical system. And you’ll streamline the path to final inspection along the way.
Allied Moulded’s range of fiberglass outlet boxes and enclosures and product engineering support can be the linchpin that keeps your multifamily project on time, on budget, and code-compliant—all while laying a foundation for future-ready electrical infrastructure.