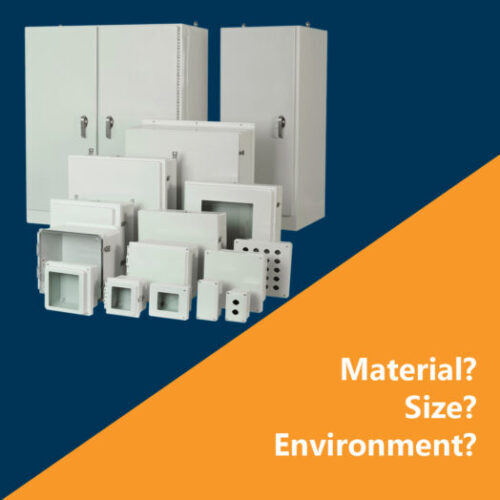
Electrical enclosures are essential to many functions, and in industrial environments, they often house critical components that allow a facility to operate. Picking the right enclosures can mean the difference between
reliable uptime and unexpected downtime, not to mention the various safety concerns.
So, how do you ensure that you have the correct enclosures for the job at
hand?Well, it can help to learn more about how enclosures are designed in the first place.
Materials
Electrical enclosure design starts with choosing a material. In general, there
are a handful of material options.
You have metals that mostly consist of aluminum, treated steals (like
galvanized steel), and stainless steel. Less often, you might also see Zinc as a choice.
On the non-metal side, polycarbonate and fiberglass dominate.
Choosing a material is fairly straightforward. Metals are very tough, so in certain exposed conditions, you’ll want a metal that can take a hit. In those cases, you also want a metal that won’t oxidize easily,
which is why aluminum and treated steels are common choices.
Meanwhile, polycarbonate boxes cost a lot less and are immune to rust and corrosion. Fiberglass costs a little more than polycarbonate, but it’s more resilient against sunlight, impact resistant like metal enclosures and fiberglass is safer in industrial settings that employ corrosive chemicals.
Picking the right material is a matter of weighing costs vs the pros and cons of each material.
Size, Shape, and Configuration
Once the material is chosen, the box itself must be physically designed. Naturally, the box has to be large
enough to hold the components that it will house, and it has to be shaped so that it can fit properly wherever
it will be installed. An electrical engineer will usually review the specifications of the job and design in an enclosure that will
fit within the specifications. The specific use of an electrical enclosure will determine how the enclosure is configured. If there are digital displays or warning lights that are part of the internal components, then a window or clear HMI Cover
would be added to the enclosure.
Environment
The last concern is often the most challenging for engineers. An electrical enclosure has to survive its own environment. Designing around this is a consideration of the entire lifecycle of the enclosure.
A quick example of environmental concerns would be an enclosure for components inside of a carwash. This is a box that will sustain high levels of exposure to moisture, possibly even jet sprays of water. The box has to remain watertight throughout its lifecycle in that environment. Any failure could be catastrophic to the carwash and even present significant dangers to people.
Environmental concerns can vary widely, but they impact more than just the material used for the box. Attachment designs, latches and opening mechanisms, and every facet of the box will be impacted by environmental concerns.